In the ever-evolving landscape of industrial automation, pneumatic manipulators have emerged as pivotal tools for enhancing productivity, precision, and safety across various manufacturing sectors. Also known as mechanical arms or robotic limbs, these advanced devices embody the perfect amalgamation of power, dexterity, and control, making them indispensable assets in today’s fast-paced industrial environments. Here’s why pneumatic manipulators are shaping the future of manufacturing and beyond.
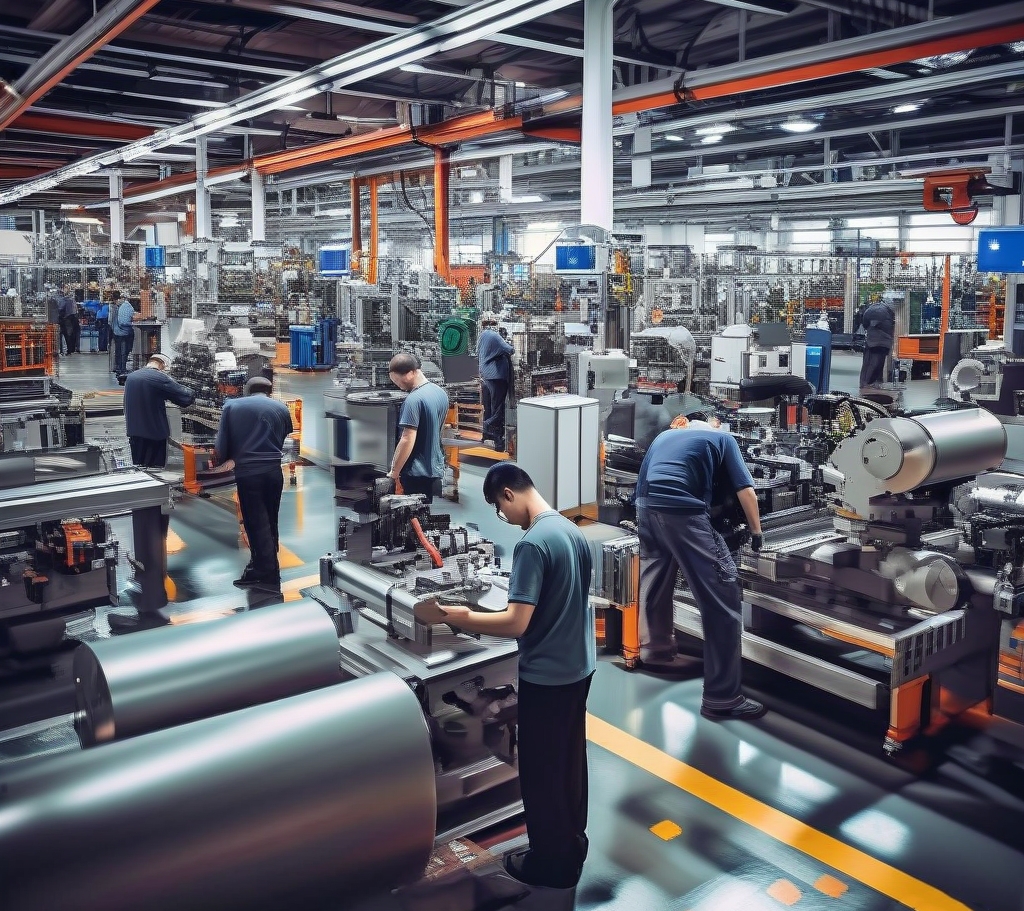
Enhanced Productivity
Pneumatic manipulators are designed to execute repetitive tasks with consistent accuracy, thereby reducing the potential for human error and minimizing production delays. These robust machines can operate continuously without fatigue, significantly outperforming human workers in tasks that require high speed and precision over prolonged periods. By integrating pneumatic manipulators into your workflow, you can achieve higher output rates and improved efficiency, ultimately accelerating your production process.
Improved Precision and Quality
In applications where exactness is crucial, such as assembly lines or quality control processes, pneumatic manipulators offer a level of precision that is challenging for humans to match. Their finely tuned movements ensure repeatability and consistency in every operation, leading to a higher standard of product quality. This reliability can help reduce waste, lower costs associated with defects, and enhance the overall reputation of your end products in the market.
Ergonomic Benefits of Manipulator
The repetitive nature of certain industrial tasks can lead to worker fatigue and injuries, impacting workforce morale and increasing downtime. Pneumatic manipulators step in to perform these physically demanding jobs, alleviating the strain on human workers. This not only promotes a safer working environment but also demonstrates a commitment to employee well-being, which can positively influence company culture and staff retention.
Increased Flexibility
Pneumatic manipulators come in various forms and specifications to suit a wide range of applications. From lightweight models designed for subtle object manipulation to heavy-duty versions capable of lifting substantial weights, these machines can be tailored to meet specific operational requirements. Their programmability also means they can be quickly reconfigured to adapt to changing production needs or new workflows—offering unparalleled flexibility in a dynamic industrial setting.
Safe Working Environment
By automating manual tasks with pneumatic manipulators, you can significantly reduce the risk of workplace accidents. Heavy lifting, dangerous machinery operation, and exposure to hazardous materials can be safely handled by these robotic systems, creating a safer environment for human workers. Additionally, their use can help comply with regulatory standards and reduce liability risks associated with workplace safety.
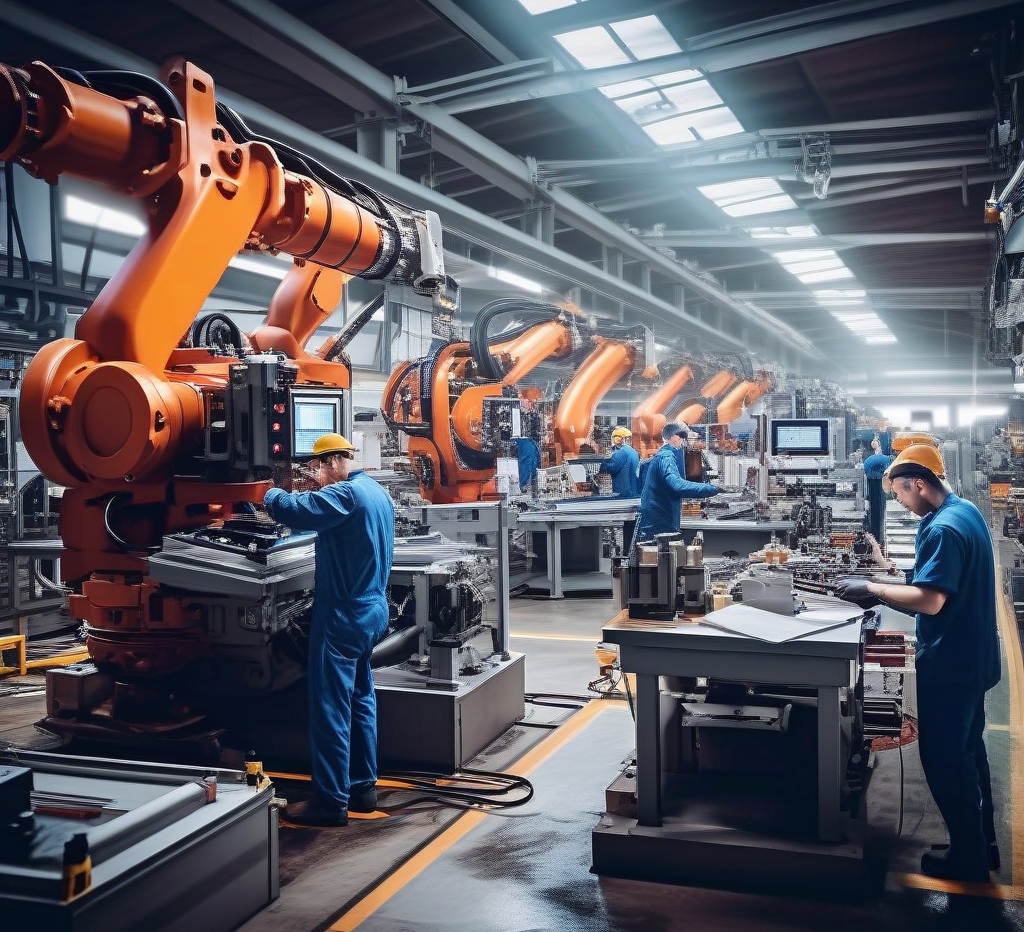